Deltec have been making calcium reactors for many years and are now on to their fourth generation with each series adding little improvements from the last.
Why Fluidise the Media
Fluidising the media allows smaller grains of media to be used which in turn creates a larger surface area which is where the media disolves. The result of this is a significantly more efficient reactor and a higher calcium output.
If the grains of media are assumed to be spherical then by halving the size of the media you will increase the surface area by 2. In reality the diameter of the grains is probably 1/10th or less that of a normal reactor so therefore the surface area will be 10 times larger and there will be 10 times more surface area for the disolving action to occur at.
Tracking
With non fluidised reactors, the media dissolves into smaller and smaller grains and form 'fines' which accumulate within the reactor. This causes the water within the reactor to track through the media following the easiest route. This action further reduces the contact area with the water.
Cleaning
With fluidised reactors the fines pass out of the reactor and the unit generally only requires a top up whereas with non fluidised types the chamber must be regularly cleaned and the media washed to remove the finer particles.
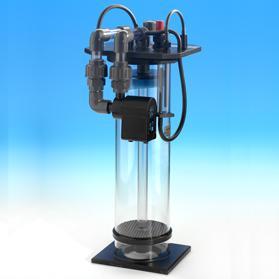